Gt40 Top Speed
The release of Ford v. Ferrari, which tells the story of Carroll Shelby, Ken Miles and Ford's quest for Le Mans glory has us going through the archives. From the October 1966 issue of R&T, please enjoy this thorough technical analysis of the car that finally beat Ferrari—the GT40 Mk II. -Ed.
There's a lot of cheer in the Ford racing organization, from Ford general manager Don Frey right on out to the errand boys in the three racing teams. After three years of trying, Ford became the first outfit to win the Le Mans 24-hr race with an American car. And win they did, in grand style with a 1-2-3, even if the finishing order of the three wasn't quite what Mr. Beebe had planned.
Why was the Ford performance so much better this year than in the two years past? Why did Ford campaign the big Mark II, rather than the lighter GT40 with the 289 engine or the more advanced "J" car? Why a slow-turning 7-liter engine instead of a lighter, high-output unit such as the Indianapolis DOHC engine? Or even the 7-liter single overhead cam?
Toward the end of 1964, Roy Lunn, Ford 's chief design engineer on the GT project, began to have doubts about the development possibilities of the basic 4.7-liter GT40. About that time Ford set up Kar Kraft—a wholly owned subsidiary intended to be small enough to get things done with dispatch appropriate to racing ways but close enough to the parent company to draw on its resources.
With Kar Kraft set up and Lunn its head, the first project of the small company was to design a new transmission. The original Colotti had been modified in 20 ways to cope with the relatively large 4.7 engine but its reliability was still marginal; Lunn felt it had to be replaced as transmission failures were still the most common difficulty.
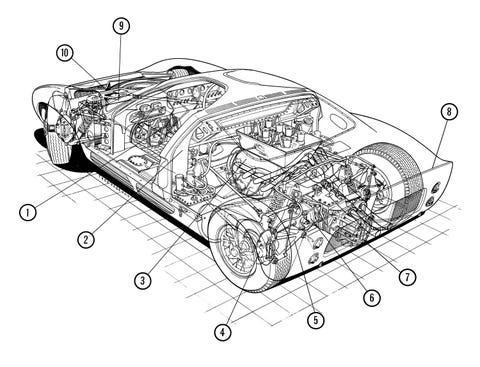
Ford
Kar Kraft's next project was to chop up two GT40 chassis to accommodate the hulking 7-liter Ford Galaxie engine. Work on these two cars was started in March 1965 with no real thought of running them at Le Mans that year. But tire developments made decent handling possible and with the first running car Ken Miles lapped Ford's 5-mi oval track at Romeo, Michigan, at 201 mph. Whereupon somebody up high said this is the car we are going to race!
If Ford people had been experienced at Le Mans, they wouldn't have tried it. They missed the April practice altogether with the 427 cars and actually finished building the second one at Le Mans just before the race, but nevertheless started both cars. What happened is well known now. Hasty preparation resulted in a gear that was intended for scrap being put into one gearbox and dirt on a bearing surface of the other gearbox, putting both the new KK transmissions out of commission. However, from the amount of development work that has been done since then, it seems unlikely that the cars would have finished anyway in 1965.
Lunn says he learned one big thing from the 1965 experience: that the big engine, loafing around at 6000 rpm, was the way to go.

R&T Archive
The New Racing Approach
John Cowley, in charge of managing the racing effort from Dearborn, wisely realized the value of intramural competition. Thus he decided to put three racing teams on the job of preparing and racing the cars for the 1966 effort. He stayed at the helm of the operation, coordinating the three teams' work and feeding information back and forth so that each team could benefit from the findings of the others.
Previously the teams had gone their own way without much central supervision. Cowley and his two aides—Homer Perry and Chuck Folger, both development engineers—pulled the efforts together while still allowing the initiative and competitive spirits of the separate teams to motivate their work.
These three men supervised most of the vehicle tests, which required a staggering amount of travel as tests were run at Daytona, Sebring, Kingman (Arizona, Ford's desert proving ground) and Riverside.
Besides the good coordination, bringing in the Holman-Moody outfit was a major factor in this year's organization. Cowley says that there was a bit of skepticism about a stock car team's ability to do the job: but H-M certainly proved their own ability at it as well as putting Shelby American even more on its toes. Furthermore, at least one highly significant engineering development that came out of Holman-Moody.
In addition to the new team structure, there was simply greater experience throughout the Ford Dearborn group. By this time the Ford people had gained a good feel for racing. There was a Le Mans Committee, made up of top personnel from the participating divisions of the company—(Engine & Foundry, Transmission & Chassis, and Ford Division) meeting regularly to discuss mutual problems and courses of correction. It all added up to a properly concentrated operation focused on one thing—winning at Le Mans. A brief outline of the people, groups and their functions:
- Donald Frey: VP and general manager of Ford Division.
- Leo Beebe: public relations & promotion, director of racing activity.
- Le Mans Committee: coordinate entire Le Mans activity.
- Jack Passino: manager, Special Vehicles Activity (all GT cars).
- John Cowley: race manager.
- Kar Kraft: design and build original prototypes. Headed by Roy Lunn, with Chuck Mountain. Ed Hull and Bob Negstad on staff, and various "moonlighting" Ford engineers.
- Race teams: Shelby American. Holman-Moody, Alan Mann Racing, Ltd.— prepare, develop and race cars.
The Mark II And Its Development
After Le Mans 1965, Ford people were sure that they had in the Mark II (as all 7-liter GTs are called) a car fast enough to be competitive in 1966. If it could last.
The Mark II was basically the same car as the original GT, which had been conceived by Eric Broadley in 1962-63 and refined extensively by Lunn's team of designers. The 7-liter engine and various strengthening components required with it added several hundred pounds of weight; it had a longer nose to accommodate more radiator and ducting, and cast alloy wheels rather than the wire ones of the original GT-40s, now called the Mark I. Conventional in layout for a contemporary GT racing car—a midship engine driving the rear wheels, semi-monocoque chassis construction, short-and-long-arm independent suspension front and rear—it was unorthodox in but one area—the large, heavy, slow-turning V-8. Lunn and his people, but not necessarily all the racing teams, were convinced that the big engine was the way to go: it was relatively cheap, well proven (in NASCAR racing) and so related to production engines as to offer maximum advertising potential. There wasn't room, by the way, for the more bulky SOHC 427. And a complete development program would have been necessary to make the Indy DOHC engine suitable for a 24-hr race.
But with the big torquer came new problems. Most directly related were power transmission components, but most perplexing was the problem of stopping a 2800-lb plus machine (with driver) from 200 mph! The added weight meant harder pounding on suspension pieces at courses like Daytona. The long nose brought on new aerodynamic problems, in the form of poor rear end stability—witness the plethora of fins, tabs and the like on the 1965 Le Mans Mk IIs. However, now there was time to think, to test systematically, to do it right this time. . .
The development program went methodically forward.
A Year Of Improvement
Engine
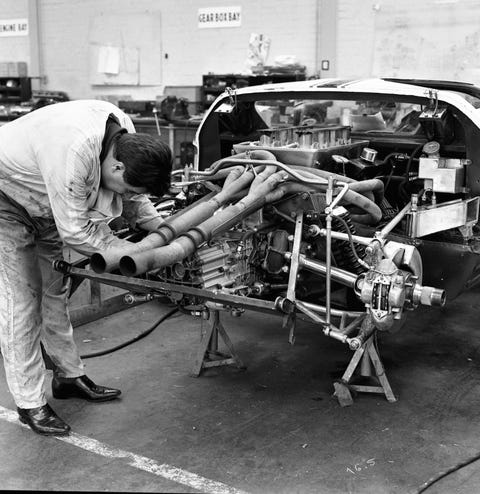
Ford
After it was apparent that the 7-liter pushrod engine was going to be used, Passino and Shelby asked for all possible weight reduction in the engine. Gus Scussel, engineer at Ford's E&F (Engine & Foundry Division) in charge of the project, achieved it with aluminum heads, an aluminum hub on the vibration damper and a water pump of the same light alloy. This comparison of engine weights is enlightening (all weights dry, less exhaust manifold, air cleaner, clutch):
- 7-liter NASCAR Version: 602 lb
- 7-liter Le Mans Version: 550 lb
- 4.7-liter GT Mk1: 432 lb
- 4.2-liter Indianapolis: 428 lb
The nice thing about using this engine, says Scussel, is that he knew at the outset that it had the durability to go 24 hours, providing the rpm range could be controlled. Thus all it needed was refinement, and to keep the speed range where he wanted it, Scussel issued a firm edict to all drivers that 6200 rpm was the limit. No exceptions, even though the engine had a safe limit of 7400 rpm for short-term use. To this end, each car's tach was accurately calibrated and a calibration chart taped in the driver's side door jamb.
Aluminum heads meant a small reduction in valve size from the NASCAR version: gauge diameter of intakes was reduced from 2.16 inches to 2.06, exhausts 1.70 to 1.625. Otherwise head design remained the same, but compression ratio was reduced from 12.5 to 10.5:1 because Le Mans fuel is only 101 octane (research method) vs. the 102.8 allowed in stock car racing. As far as octane requirement is concerned, the 10.5:1 aluminum head is about equivalent to a 10.0:1 iron head because it conducts heat away faster. The regular "hi-riser" intake manifold was retained.
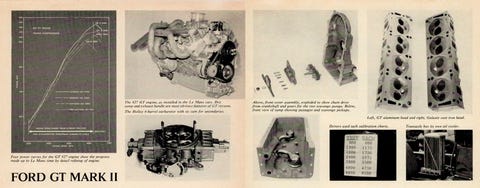
R&T Archive
Aside from the aluminum heads, the most important change for GT use was a dry sump. This was completely redesigned this year by E&F and has two scavenge pumps driven by an internal chain from the crankshaft, replacing last year's one pump driven by an external, toothed belt. The pressure pump is gear driven from the camshaft and produces 65-70 psi at 6000 rpm. The oil cooler is a NASCAR item also; cooling is so effective that in cool weather it's necessary to blank off parts of it. Maximum oil temperature under any conditions encountered so far has been 250° F.
Tailoring the engine for the GT also included devising a suitable exhaust system, and carburetion. With the exhaust it was simply a matter of getting the required length of pipe for every cylinder and fitting the resulting bundle into the small space available. Not so simple, after all—there are many (trial and) error bundles lying around the buildup shops!
Somewhat surprisingly, the carburetion settled upon was a single 4-barrel Holley unit, rated at 780 cu-ft/m in flow. This looks odd among the multiple Webers of competing cars, but apparently does the job well. E&F wanted vacuum-operated secondary throttles opening, but Ken Miles won out and got mechanical opening. This is accomplished by a cam-and-rod arrangement designed for equal opening, primary and secondary.
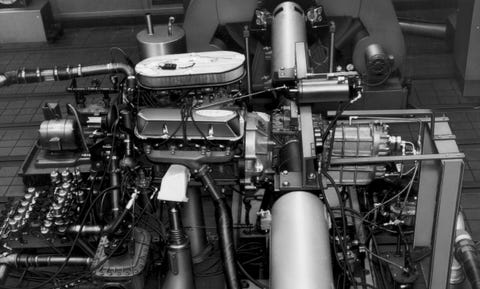
Ford
Durability testing was thorough in the usual Ford way. Ford dynamometer facilities are extensive and comprehensive, able to accurately duplicate any driving pattern through computer-programmed changes of speed, load, and throttle opening. After preliminary test runs by drivers in an elaborately instrumented car (measuring and recording on an oscillograph such things as engine speed, manifold vacuum, rear wheel speed, throttle plate angle and axle shaft torque) it was comparatively simple for Ford dynamometer people to reproduce the track conditions on an engine test stand. The dynamometer cycle allowed 6800 rpm in 1st and 2nd gears, 6250 in 3rd and top, and was run for 48 hours—as compared to the 6200 limit for drivers and about 38 hours normally put on a given engine (4-hour break-in, 4-hr vehicle sort-out, 6-hr practice, 24-hr race). Thus at race time durability wasn't a question mark in any sense.
In its Le Mans form, the engine is anything but a high-output unit. At 485 bhp (the NASCAR version produces 520 bhp) it produces only 69 bhp/liter, far below the 100 bhp/liter now achieved almost routinely in high performance engines. It runs about 2000 rpm slower than competing engines and will pull smoothly from 1000 in top gear! It is inexpensive to boot, and it is a great achievement to have taken a basic sedan engine and won Le Mans. Complete specifications will be found in accompanying tables.
Transmission
Getting the tremendous torque of the 427 engine to the ground has been a real challenge for the Ford engineers. However, the problems have been solved and transmission failures are no longer a problem with Ford GTs. Kar Kraft conceived the present transaxle assembly; it is a light-alloy encased unit making maximum use of available heavy-duty Ford gears and shafts.
A Long 2-dry-plate clutch, each plate 10.0 inches in diameter, transmits torque to the input shaft of the gearbox; a production 4-speed synchronized gearset takes over from there, and finally a set of transfer gears takes the torque to the output shaft. It is the transfer gearset that is varied to give different final drive ratios: the differential ring gear and pinion are always the same at 3.09 (34/ II). In the case of the Le Mans Mk II. The transfer gearset is 0.899:1 for a final drive ratio of 2.77:1. The four gearbox ratios are 2.22, 1.43, 1.19 and 1.00:1.
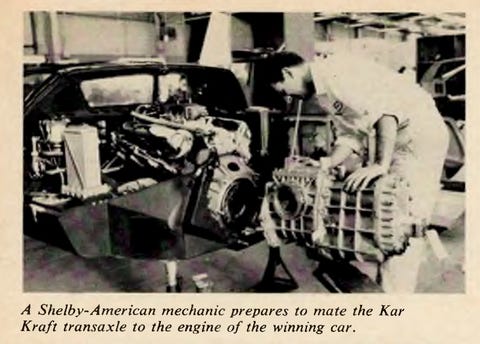
R&T Archive
Kar Kraft is busy with automatic transmission design and development, now that the manual is working so well. There are two types currently under study. Both are 2-speed plus torque converter with manual shifting. The simpler of the two, lighter than the 4-speed manual, is similar to the Chaparral unit with a dog-clutch synchronized spur gear box. This type requires lifting the throttle foot for upshifts and judicious coordination for downshifts—allowing some room for error on the driver's part. The other is a "power-shift" type, which is bulkier and heavier but allows upshifting and downshifting under full power. Again, this is a constant-mesh spur gear box but is shifted hydraulically by oil pressure and disc clutches; the driver's lever operates valves only. It was this unit that was used in one car at Daytona (ran 14 hrs) and Sebring (finished). The torque converter in either transmission is from a Falcon Six, with strengthened vanes, has a stall speed of about 4200 rpm and a maximum multiplication of 1.9:1. For a race like Le Mans, first gear would be about 1.45:1 for an upshift speed of 135 mph. But neither of the automatic boxes is up to Lunn's expectations yet, and development work continues. He is hoping for a maximum power loss of 3-4 percent, rather low for a torque converter. The typical loss for a modern passenger car automatic, which includes a larger hydraulic circuit for automatic shifting of planetary gearsets, is about 8 percent.
Chassis & Suspension
Changes to the chassis structure have been for convenience and strength. New jacking points at the rear are now the same as those at the front—made possible by the new body shape at the rear. Daytona tests produced cracks in engine mounts and in the structure around the front A-arm pivots, so gussets were added in appropriate places. A-arms up front were increased in diameter, and new front upright castings were designed with greater wall thickness and bearing area, and some internal ribs. The pivot point for the rear upper control arm is now supported at both ends instead of being cantilevered, and the control arm length now can be adjusted without removal. New wheels also resulted from the Daytona tests— they have heavily reinforced spiders. Modifications to date bring the chassis' torsional rigidity to 10,000 lb-ft/degree corrected to the usual 100-in wheelbase. Most of this development work was carried out by Shelby American.
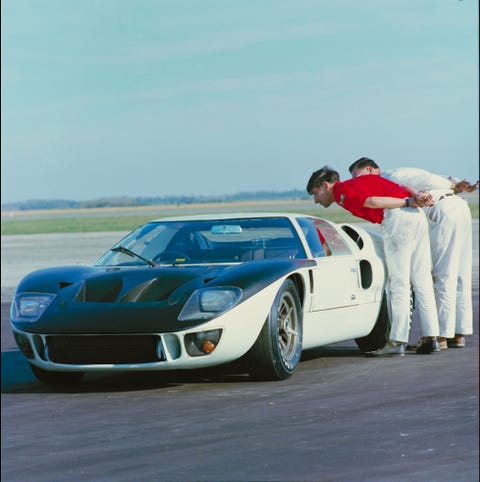
Ford
Roy Lunn says that Ford has stolen the lead in handling and aerodynamics—"If Chaparral and Ferrari had mastered these, we wouldn't have seen them, with their drastically better power/weight ratios!" Again, these achievements have been made possible by Ford's vast engineering resources. For instance, suspension geometry doesn't have to be plotted out on paper time after time until the desired combination is obtained; rather, the computer in effect does this work thousands of times faster than human beings can. Aerodynamics have been studied in the Ford wind tunnel, capable of 130 mph, and checked out on Ford proving grounds under 200-mph steady running. Impressive though Chaparral facilities are for a small outfit, they can't be equated with the vast resources of Ford even if GM help is coming in.
Rather than any revolutionary suspension improvement, then, we must say that suspension geometry of the Ford has been refined to the teeth by the fast trial-and-error of the computer, and as usual fine-tuned by the driver's seat-of-pants. Koni double-adjusting (separate adjustment for jounce and rebound) shocks replace the Armstrong units formerly used. Wheelbase remains the same as the Mk I at 95 inches, tread is increased 1 inch to 57 at the front and remains 56 inches at the rear.
Brakes
As noted before, brakes have been a sticky problem. Nobody at Ford or Shelby American will say that the brakes are adequate yet—but rather that the driver must be careful with them. Last year the radial-spoked rotors (vented discs) cracked regularly. Curved spokes this year have reduced failures somewhat but not completely, and metal coatings tried earlier failed to live up to expectations. With 653 square inches of swept area, there is no room for larger discs or pads. What happens in use is that the rotors get tremendously hot during braking and then cool very rapidly as speed builds.
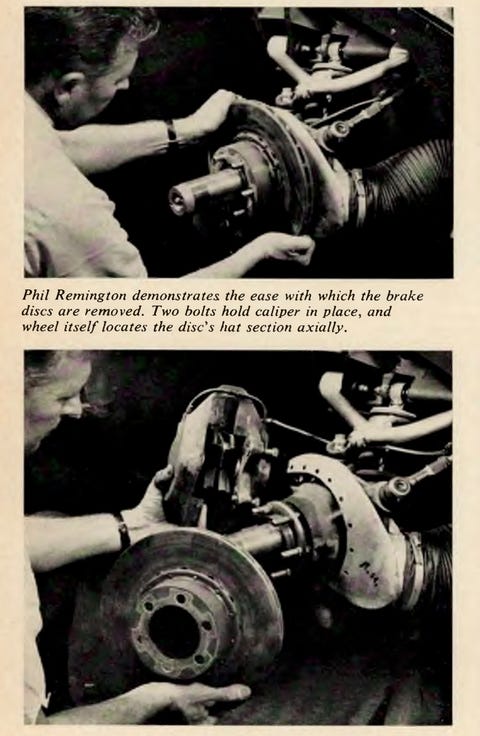
R&T Archive
Because pad wear and rotor cracking were insoluble, at least for this year, it seemed that methods had to be found for replacing brake parts quickly. Two neat solutions along this line came forth from the racing teams. Shelby American head Phil Remington devised quick-change brake pad retainers which allow rapid removal and replacement of the pads. A remarkable new feature was conceived by John Holman of Holman-Moody during the year's development: quick-change discs! This is a first, and surely will start a trend. The disc hats are outboard of the hub flange and held in place by the wheel studs, the caliper and the wheel itself. Thus when the wheel is removed, and the caliper swung away (which requires only the loosening of two bolts), the disc may be snatched off and a new one slipped on in seconds. Design details and development work on this item were carried out by Ford and Shelby American engineers. Disc diameters remain 11.6 inches front and rear, and Girling BR single calipers are used at both ends of the car.
Body
Only the midsection of the Mk I body remains the same in this year's Mk II. Front and rear sections are completely new and it is a tribute to their designers that absolutely no add-on tabs, fins or the like were needed this year. Only the adjustable spoiler at the rear was needed, and this was set at heights from 1.5 to 3 inches to suit different drivers.
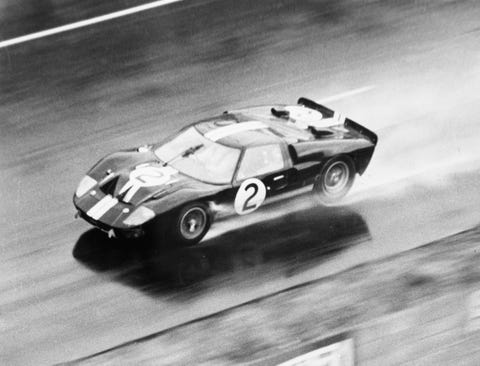
Ford
The most striking body change is the front end. It is 9 inches shorter than last year's nose and is actually a "production" GT40 nose with slightly higher fender humps for more wheel travel. Wind tunnel work, and Phil Remington's engineering intuition, said that the nose had to be as low as possible. And the shorter length gets the center of pressure back toward where it should be. The front end, therefore, is responsible for the lack of fins on the rear. It also saves 19 lb.
The wind tunnel was used to develop new ducting for improved engine, transaxle and brake cooling, and the new duct disposition is thus:
- Side Scoops:
- Low, right side: transaxle
- Low, left side: engine oil
- High, both sides,
- Upper two-thirds: carburetor
- Lower third: brakes
- Top Deck Scoops—added at Sebring: brakes
Louvers in the center of the rear deck direct air over the exhaust pipes and get that hot air out. The new tail weighs 37.5 lb verses 80 for the old one. Other body improvements have been for convenience, such as a new access panel in the nose for getting at the spare tire and oil tank. Before, the whole nose had to be lifted.
Mark II Driving Impressions, By Ken Miles
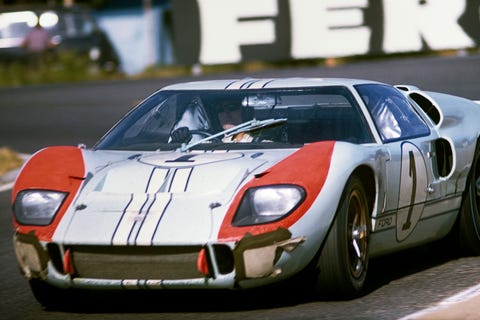
Bernard Cahier Getty Images
"When properly set up," Ken Miles says, "this is the easiest car in the world to drive. If not, it's awful—but then, this is typical of any really modern racing car. Small changes in chassis tune produce large changes in handling. The suspension is designed for a particular ride attitude; as speed goes up this attitude changes. We spent two days getting the car to handle right at Le Mans, found that the spoiler setting needed to be 2 inches, not 1. Most critical thing is precise control of rear suspension geometry with 4-link arrangement used today—tires are still an area of much ignorance—even after arriving at basic suspension geometry with help of IBM, I have to get it adjusted on the track.
"It's a cooking engine. I can lug it down to 1000 rpm in 4th. When does it come 'on the cam?'—oh, about 3000 rpm! We babied them. The thing's safe for 7400 rpm, but we never exceeded 6200 in the race.
"It's a bloody oven inside! It takes a fair amount of physical effort to drive—steering is heavy—you brace yourself in banked turns so you can hold onto the controls. This is due largely to the fact that the car has been developed so far past its original state. The steering feeds back quite a lot, and I get big blisters. . .
"Cornering is pretty neutral, takes severe provocation to hang the tail out, and then it's only briefly. She really wants to stay put. I say neutral, but that's my car. Ron Bucknum likes a little noseplow, Lloyd Ruby wants the tail hanging out—we get three different patterns of tire wear.
"The gearbox is easy to shift after broken in and has completely unbeatable synchro. It could be lighter if it weren't built around Galaxie internals, has an extra shaft to bring drive back through.
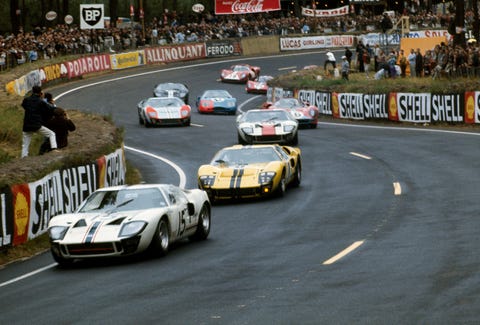
Klemantaski Collection Getty Images
"Brakes are high-effort. Can't possibly lock wheels. They are our Achilles heel; there's just not room for a brake big enough. Running 1650° F, there's too much variation in temperature— I planned my driving so only one disc change would be necessary. Unfortunately, one of the new discs was bad and I had to stop again. At the end of the race, this set was in good condition, ready for another go.
"The seating is very comfortable, yes. Hard to get into, but no aches at all after the race. For rear vision, pick the mirror glass off the floor and hold it in your hand. The wipers work well at high speeds, but the washer hardly works at all.
"Throttle linkage is very important. It must achieve two things: it must be smooth, and progressive—slow at first opening, getting faster. I have these qualities, but I don't like the suspended pedal. Not natural."
Riding with Ken, I found that indeed the Mk II is a flexible car. It isn't quiet, of course, but with the big noises going out the back it's not horrendous; the ride is about that of a street Cobra. There 's a realization of great structural strength, but there are rattles all over. And it is possible to lug from 1000 in 4th. Acceleration in the indirect gears, once past 3000 rpm, is simply indescribable.
Summary
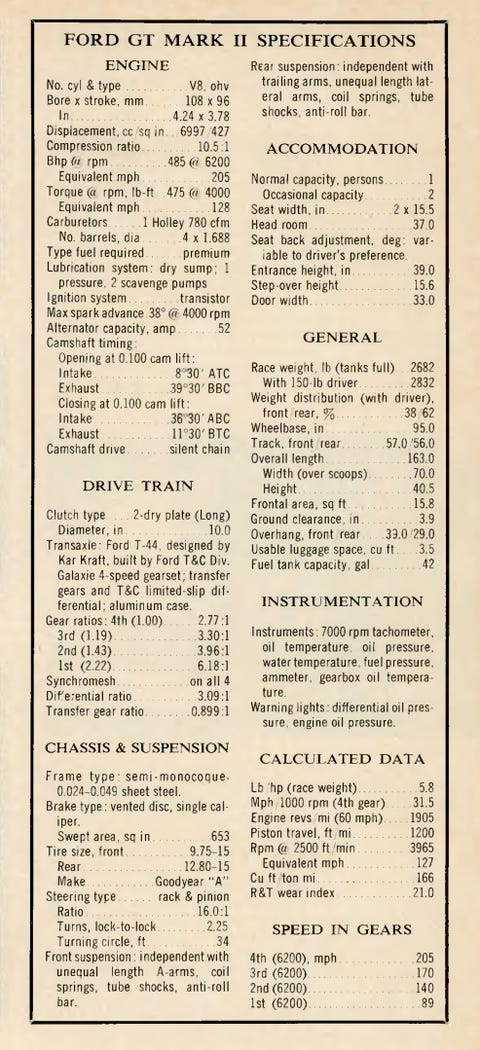
R&T Archive
The Ford GT Mk II, though its beginning was in England, has evolved into a distinctly American car. Contrasted to its contemporaries, it compares with them just as an American sports car does with European ones—the big point of difference being that the American car has a relatively heavy, large-displacement and slow-revving engine with unsophisticated valve gear. For the first time it proved that this power concept can be fully competitive with the light, high-output European engines in a long distance race like Le Mans.
If Ford is to continue racing, and it appears fairly likely that the company will, it is the new "J" car that will be campaigned as the prototype car. It is the logical evolutionary step from the Mk II, but having been drawn up on a clean piece of tracing paper, with the 427 engine designed in, it embodies all the Ford people have learned in their three years' experience with the GTs.
Miles and Ruby drove an open car at Sebring that was a prototype for the J car: it had a single-sheet aluminum underbody, which wasn't quite satisfactory but which pointed the way toward using the honeycomb aluminum structure the J car now uses. As a result of the use of this material in bulkheads (as well as other new structural efficiencies) the weight of the J car's underbody is only 169 lb, versus 360 for the Mk II's single-sheet unitized steel underbody.
Back at Ford Dearborn, out there at Shelby American, over there at Alan Mann and down there at Holman-Moody, everybody has crossed fingers. At this writing it was budget time in Dearborn. We all hope the budget says "go."
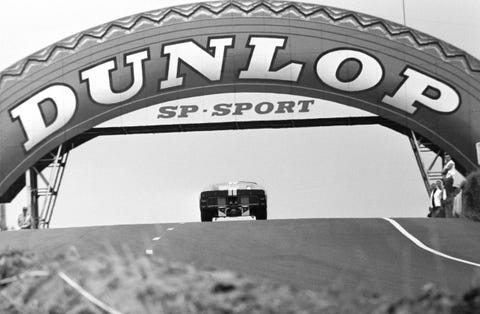
Ford
This content is created and maintained by a third party, and imported onto this page to help users provide their email addresses. You may be able to find more information about this and similar content at piano.io
Source: https://www.roadandtrack.com/motorsports/a29798198/ford-gt40-mk-ii-le-mans-analysis/
Tidak ada komentar:
Posting Komentar